Transporting glass loads requires extreme caution. Especially
when the loads take on the dimensions of a small bus.
This calls for transport trolleys that demonstrate outstanding manoeuvrability and guarantee the physical well-being of the employees. For renowned glass manufacturer and processor INTERPANE, we have therefore developed a foot protection system that represents the highest level of work safety and at the same time enables trouble-free transport of the glass panes.
The starting point
The One World Trade Center in New York, The Marq in Singapore and One One One Eagle Street in the heart of Brisbane, Australia, have one thing in common: Their façades are made of glazing from the INTERPANE Group. The company is a subsidiary of AGC Glass Europe, which belongs to the Japanese glass company, Asahi Glass Co. Ltd. The company employs 50,000 people worldwide.
INTERPANE’s product range includes float glass, low-iron glass, high-quality coated thermal insulation glass, soundproofing and solar control insulating glass, safety glass, glazing for architectural design and products for solar applications.
The company supplies glass elements for regional and international large-scale construction projects as well as for the local window construction market. They also are one of the few manufacturers worldwide to produce coated glazing with remarkable sizes up to 18 metres in length, 3.21 metres in height and pane thicknesses of up to 20 millimetres.
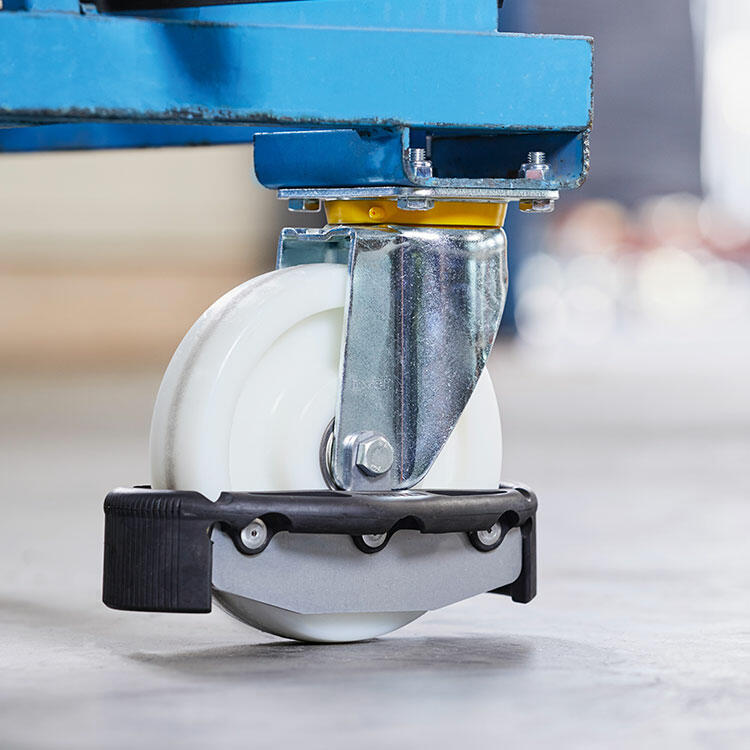
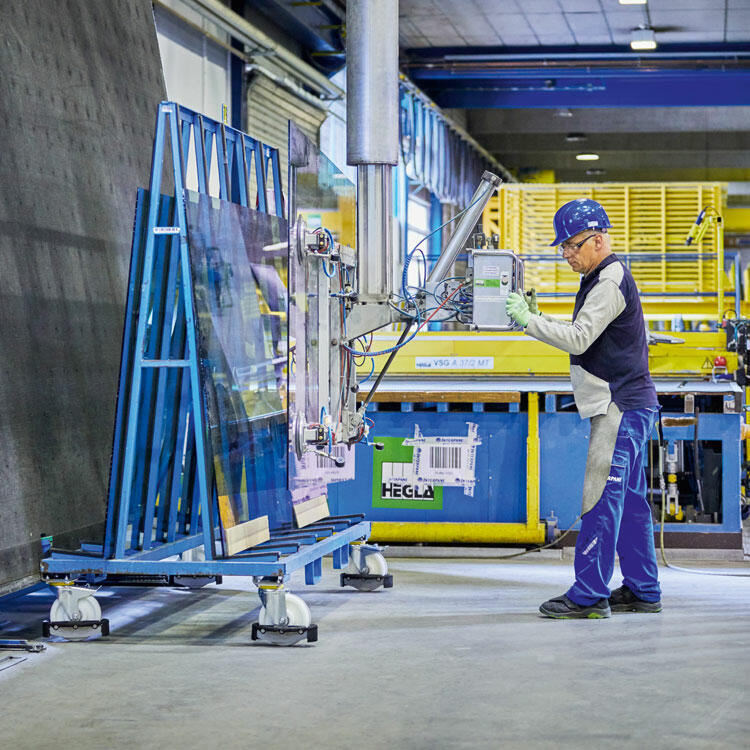
The challenge of protecting feet
INTERPANE attaches great importance to health and safety at work when manufacturing and refining its glass products. The company has announced a proactive, zero tolerance strategy. With this strategy, the glass manufacturer is pursuing its goal of preventing accidents at work, protecting the health of its employees in the long term and raising awareness of risks. All of the processes are planned and optimised accordingly, regular risk assessments are carried out and all accidents are analysed in detail.
Naturally, this also applies to the transport of the glass panes, some of which are up to 20 square metres in size. In order to ensure safe transport during the production process, the raw glass is cut to size according to the customer's requirements and loaded onto transport trolleys. Depending on the order, the panes can be up to about seven and a half metres long and around three metres high. Not to mention, their total weight can be up to 2.5 tonnes.
This presents a particular challenge in terms of operational safety. If the heavily loaded transport trolleys move too quickly or get caught on obstacles or uneven surfaces, they can bump into the employees' ankles or run over their feet. In order to prevent injuries, INTERPANE has so far used two different foot protection systems, neither of which could meet the stringent safety requirements or cope with the conditions in practice: A rigid system was found to be suitable for transportation on level floors, but as soon as the trolleys hit unfavourable ground conditions, the foot protection soon came into contact with the ground. The result: Abrupt stopping or even tipping of the transport trolleys.
The flexible protective device also posed a similar risk. This device could be drawn under the wheels and stop the castors. Both models thus posed a danger for employees and for the goods being transported. The glass manufacturer therefore needed a foot protection system that would ensure maximum safety in accordance with the company's preventive strategy.
In order to mitigate the acute danger, we reacted quickly by providing a robust metal foot guard, which also significantly improved the handling of the trolleys. At the same time, we started developing a completely new foot protection system to set new standards in safety and mobility for glass production and assembly.
Our aim was to achieve maximum flexibility for driving over uneven surfaces and other obstacles, while also ensuring maximum stability, in order to prevent any contact between the foot and wheel. With this in mind, we developed a perfect combination of rigid steel elements and flexible natural rubber. In order to provide optimum protection for the employees, flexible aprons made of rubber with a Shore hardness of 80 are fitted in front of and behind the wheel of the transport trolley. The aprons are shaped in such a way that they are pressed in towards the wheel as soon as the wheel comes into contact with the foot. This prevents the castor from moving over and crushing the foot.
The second safety feature is based on rigid guard rails attached to the side of the wheel. These ensure that the foot is guided safely around the side of the wheel. Thanks to these two elements, the feet are well protected at every conceivable angle of contact. At the same time, all floor conditions can be overcome without difficulty – and the precious glass elements can be transported safely. The solution fulfilled the company’s expectations to the fullest extent and was recommended by the INTERPANE Group’s safety coordinator for use in all of the factories.
"With TENTE's solution we have improved both occupational safety and the protection of our products."
Tobias Rüther, Corporate Safety Coordinator of the INTERPANE Group
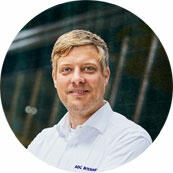
During the development process, we naturally also considered the thermal conditions that play a role in the production and assembly of glass elements, and indeed in almost all other areas of industrial production.
So our mobility solution is suitable for use at minus 40 degrees Celsius and up to 80 degrees Celsius.